In Western India, where block printing is still quite widely done, the finest examples of the technique are practiced by a few craftsmen who have mastered the craft over generations. Wooden blocks made of locally sourced teak, are soaked in oil for fifteen days to soften the timber and prepare the wood for carving. Using special tools they have created themselves, master craftsmen hand-carve patterns in relief on each block, removing the wood in the areas that do not get printed. The lines of wood left to create the print in a pattern can be extraordinarily fine. It requires great skill to make sure that each chisel stroke is precise and that no bit of wood chips off. Any error in carving implies that the block will have to be discarded, as the resulting print will not be accurate. An intricate block can take a craftsman up to one week to carve and each colour in a pattern requires a new block to be carved.
‘Varana’s block-printed capsules showcase an extraordinary process, which is art and craft in equal part.’
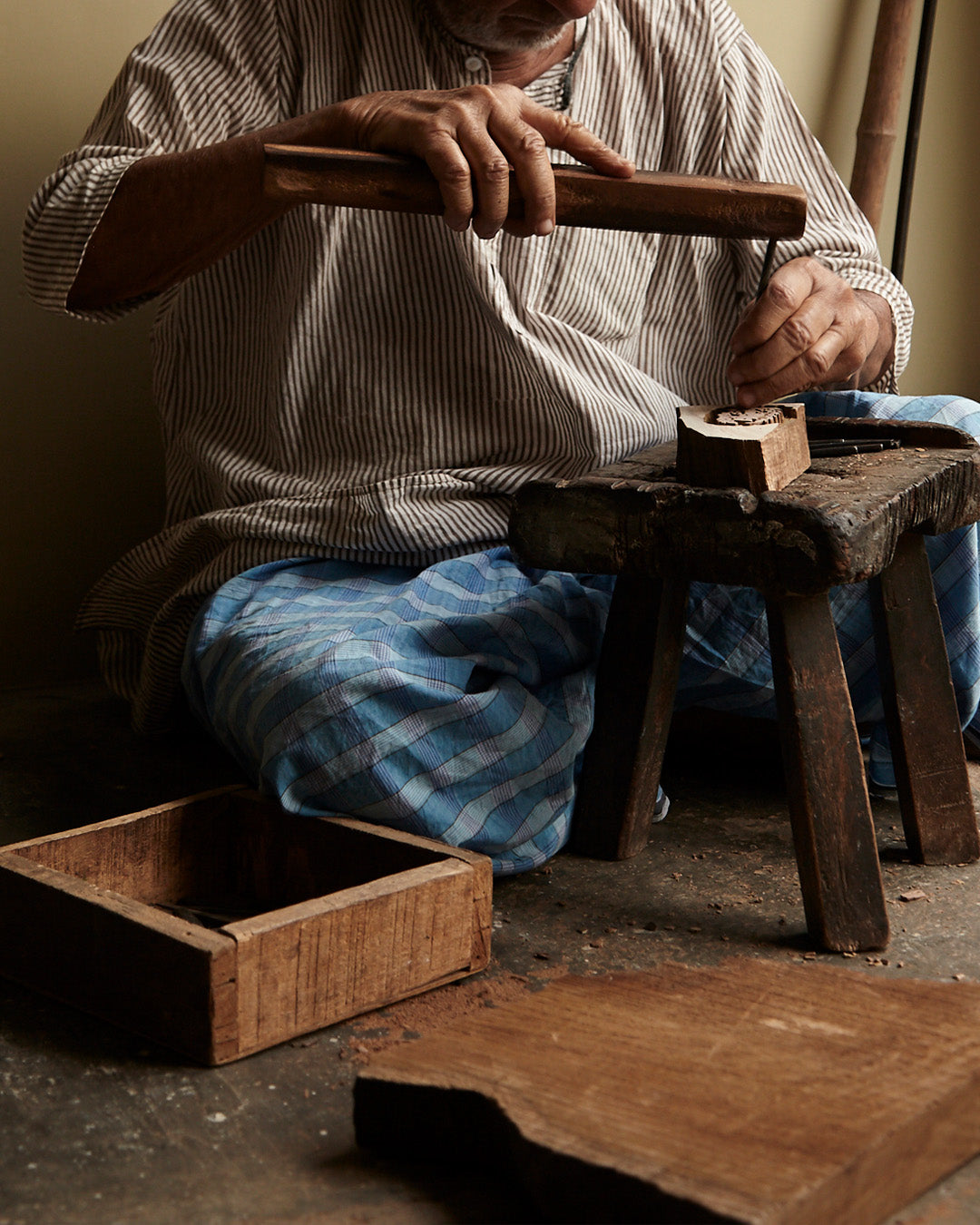
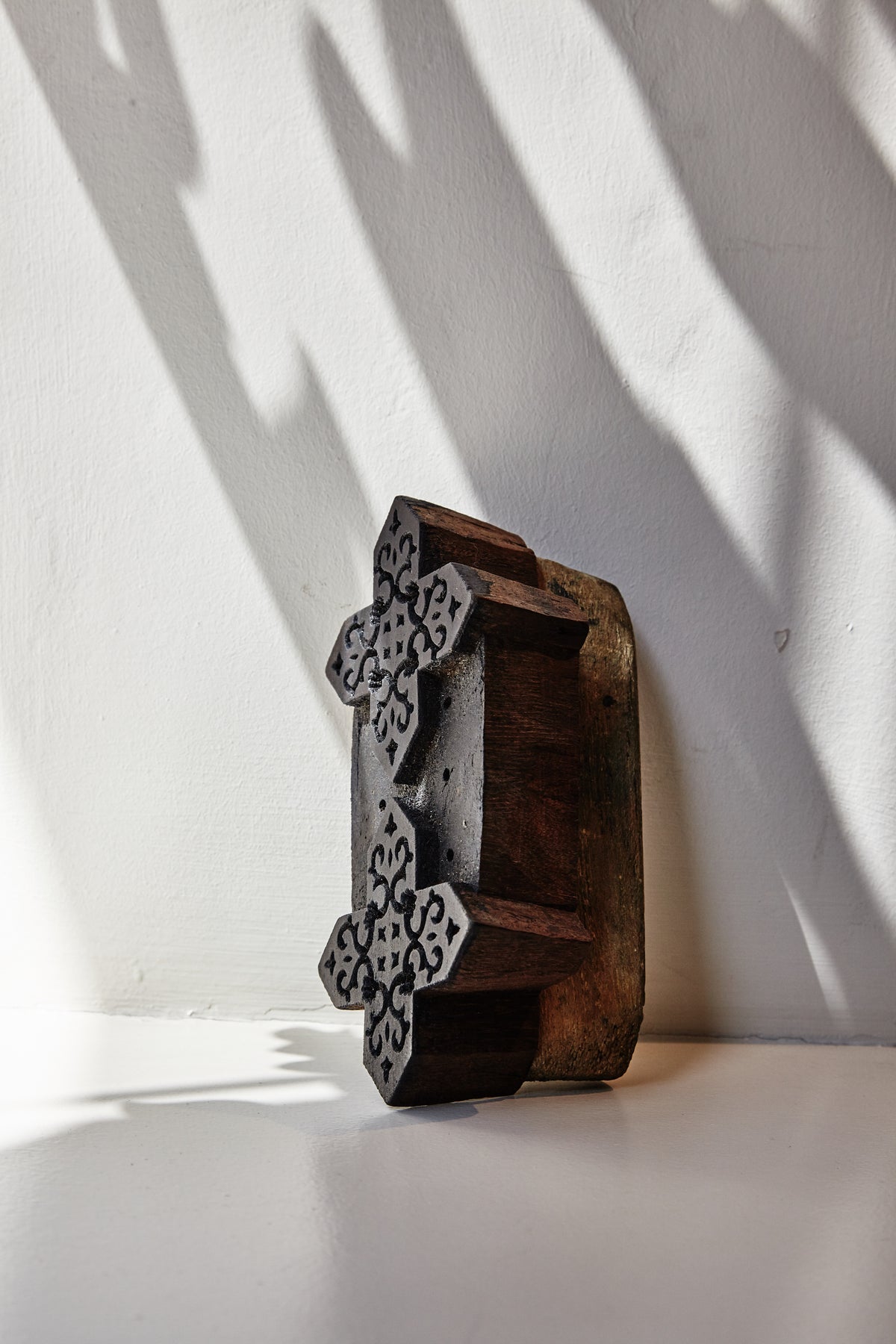
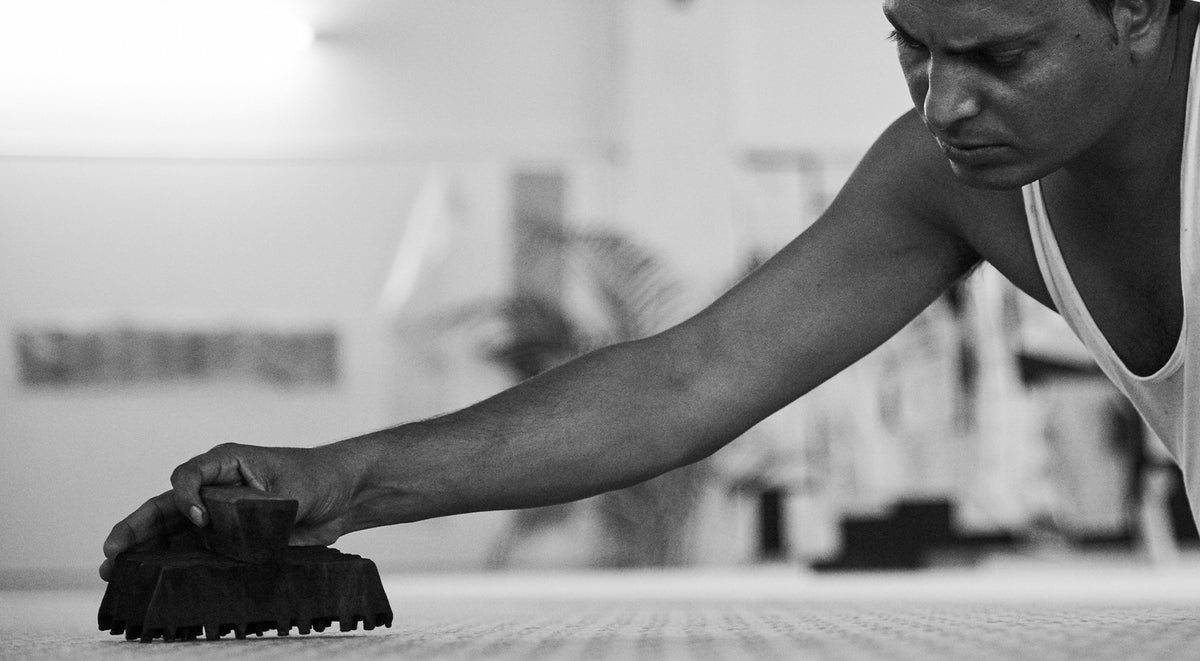
Once the wooden blocks are ready, a team of artisans carefully inks each one by hand and stamps it on the stretched fabric to create the print. Varana’s printing is done by the most skilled of craftsmen, as registering a complex design with many colours requires great mastery. The lead craftsman usually prints the outline, followed by others who fill in the details. The pressure of the stamping must be even to ensure uniformity of colour. The process is slow and painstaking, almost meditative, and requires breath control as well as perfect hand-eye coordination. As the print emerges seamlessly from the rhythmic stamping, it seems impossible to believe that the near-perfect patterns have been created by hand.
Once the whole length of fabric is printed, there is a process to fix the dyes. First, the fabric is dried in the sun. Once dry, the fabric is rolled in paper and steamed in special boilers. After steaming, the fabric is washed, dried in the sun again, and ironed before it is ready for use. Varana’s block-printed capsules showcase this extraordinary process, which is art and craft in equal part.
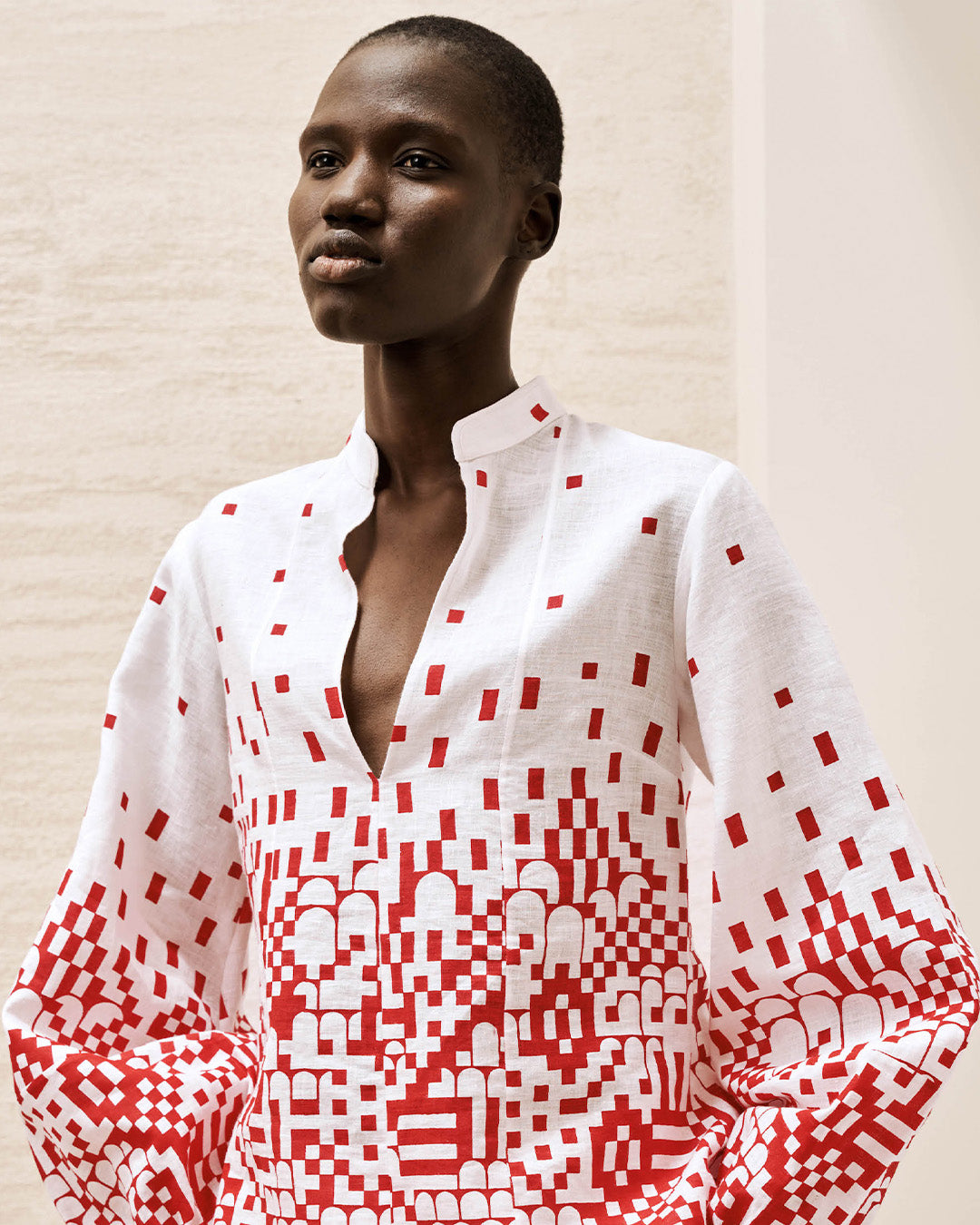
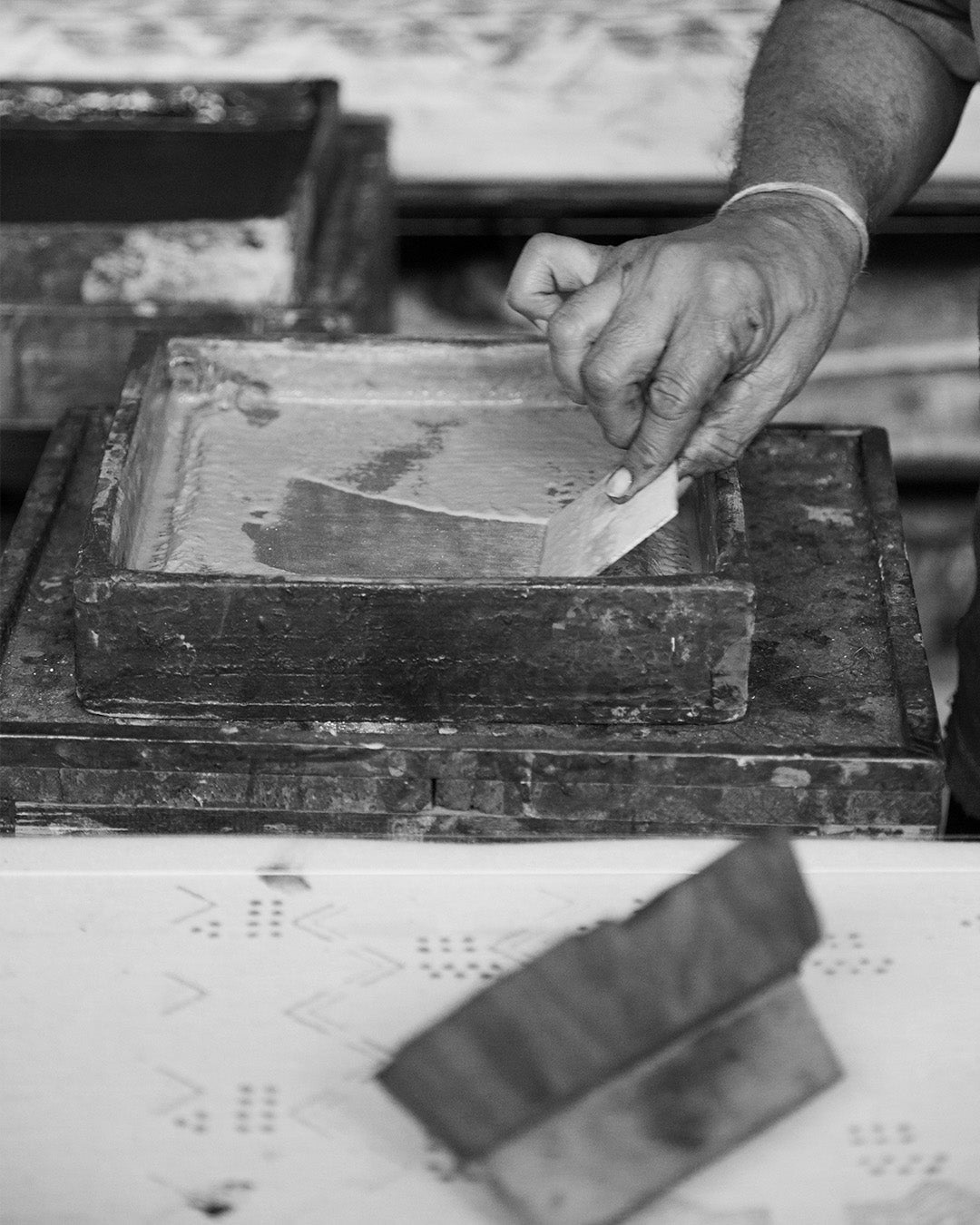
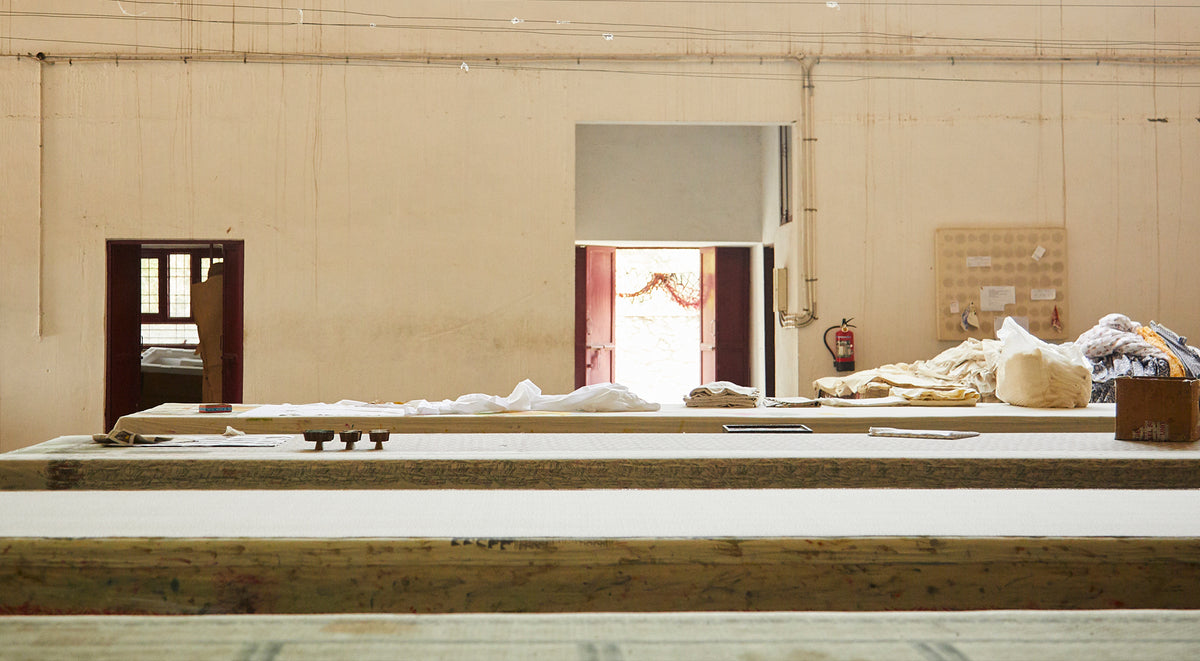
